Case Studies
ANZCO Foods applies computer vision to lighten the load
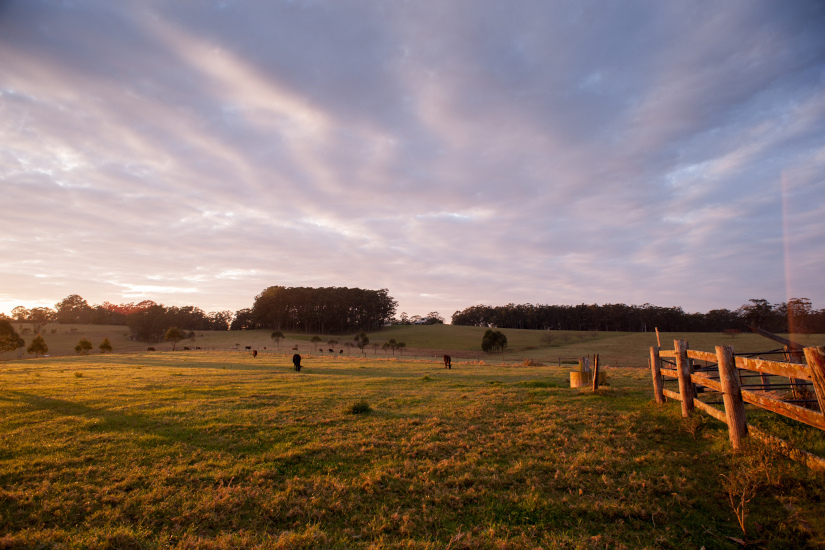
Exporting is a high-stakes business. More than simply getting products to international markets on time, Kiwi exporters face significant financial penalties and costly delays when product documentation fails to comply with international and market specifications.
Looking to improve compliance by minimising carton count errors and automate the creation of shipping documentation and compliance, ANZCO Foods turned to Leaven (now CCL) to apply foundational AI in a way that worked for the people doing the heavy lifting.
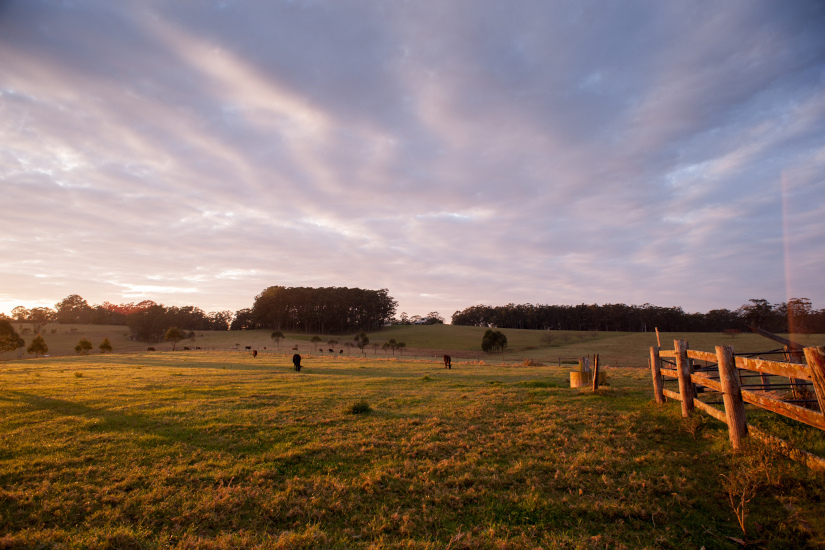
“The process was a shoo-in for AI. CCL brought knowledge and experience with the technology to develop the platform.”
Terence Kruger
Development & Innovation Manager, ANZCO Foods
ANZCO exports $1.78 billion worth of premium beef and lab products annually to customers in more than 80 countries. Every day, the company fills hundreds of containers with boxes of product in eight processing sites across the country. The exporter’s compliance teams capture and crosscheck information in shipping manifests and export documentation to satisfy customs requirements and ensure swift processing of containers at landing ports.
Accuracy is critical. If local customs agents detect discrepancies between box quantities specified in ANZCO paperwork and actual box numbers, the container is returned for unpacking and repacking. Worse, should the container reach its final overseas port, it could be rejected and must be either returned to New Zealand or its contents sold at a significantly reduced price. Both scenarios are disastrously costly and can lead to a suspended export license.
Carton counting ripe for automation
Terence Kruger, ANZCO’s Development & Innovation Manager, together with the company’s compliance team, were convinced the company’s carton counting and compliance processes could benefit from automation. The question was, how?
When they saw CCL’s handiwork at client Fulton Hogan – a project combining video capture with machine learning to make road surface inspections safer and smarter – Kruger believed AI was a shoo-in for the tedious and error-prone process of carton counting and manual compliance paperwork.
Two people at each ANZCO loadout site count boxes as they stack them in containers. Stackers use their iPhone to take a photo of each completed row, producing around 22 photos per container. An onsite compliance clerk reviews the photos saved in a shared folder, counting the number of cartons in each photo to verify a match with the shipping manifest. Once verified, a quality control administrator at ANZCO’s head office recounts the cartons in each photo to finalise and approve the container for dispatch.
It’s laborious work, requiring a dedicated FTE to verify box counts at head office, additional resources to complete shipping documentation, and two others to unpack and repack containers flagged for recounting.
Counting on AI
With AI as the foundation, the project team approached solution development with the end in mind: reduce human error from carton counting; minimise imputed information in shipping documentation; and release human resources for other tasks. The solution took shape as CRIB – container recognition, inspection, and box counting – an AI-driven iPhone app that applies computer vision to carton counting and verification. Carton stackers us the app to take a picture of each completed row of stacked boxes, and other compliance related images, including pictures of container numbers, closed container doors, and the customs seal.
A machine learning platform, based on Microsoft Azure, processes individual images to generate row counts and a total box count for each container – a process that takes a little over three minutes. This small piece of automation, alone, has shaved an estimated 45 minutes from the load time of each container. What’s more, real-time verification further reduces the opportunity for miscounts or incorrect documentation going unnoticed.
The art and science of deriving data from digital images
CCL developers applied a field of AI called computer vision, which derives meaningful information from digital images, enabling machines to recognise and classify certain characteristics contained in images with far greater speed and efficiency than humans. The model annotates images, building datasets for continuous training and improved accuracy.
Box counting sounds like a straightforward exercise, but it’s not. And while machine learning models improve and mature as they team themselves to look for the right attributes, developers must consider a range of environmental factors to make the model work.
CRIB’s development faced unique visual challenges. Packers at each ANZCO’s loadout site worked differently. Some boxes are hand-stacked while others arrive on pellets and are wheeled or slid into containers. Boxes come in different dimensions and can end up facing different directions and in rows of varying height. Light can vary inside each container, surfaces and walls create shadowing, and box facing can present at oblique angles. Visual translation must normalise these variables to ensure the model remains accurate.
More than just carton counting
CRIB is being further extended to do more than simply count cartons. Platform automation will eventually populate shipping documentation, drawing on information in company databases and cross-checking manifests with box counts and images from shared folders to eliminate pages of manual form filling.
Ultimately, CRIB will backend a compliance portal, ensuring ANZCO’s compliance team can search orders, relate associated shipping information, and provide irrefutable image-based evidence to counter spurious claims relating to incomplete or inaccurate orders.
The Azure-based platform draws on serverless compute for image processing – an approach that runs code in response to events, automating the management of underlying compute and infrastructure resources.
Carton stackers rate app
CRIB has so been trialled at ANZCO’s Rangitikei processing site and is set for rollout to the company’s remaining seven sites. User feedback has been extremely positive. “Our users aren’t technologists, so we had to nail it the first time,” Kruger said.
In addition to faster container loading times and speed of compliance, the pilot also confirmed that ANZCO will release one head office FTE from the process of carton counting. The app will also ensure everyone works in a consistent way to create more uniform shipping documentation, further reducing miscounts and imputed data in shipping documentation. “AI is an effective way to reduce costs and streamline manual tasks,” Kruger said. “It’s far more efficient to have everyone working the same way. We’re processing thousands of containers every week, so the cost of inaccuracies and non-compliance is potentially huge.”
More Case Studies
Video and AI crafts data-driven insights for the commercial fishing sector
Discover how on-board footage capture, 4G wireless transmission, and an AI-powered cloud platform is helping to modernise the...
How Endpoint Protection Transformed Fulton Hogan’s Cybersecurity
Delivering high-quality infrastructure relies on smart people, robust systems, and a smooth-running digital engine room. With an...
QLDC deploys Azure landing zone framework
Public cloud platforms and services have huge potential for organisations embracing work-from-anywhere practices. But as much as...